Anatomy of a failure (Z31 coilover adapters)
1 post
• Page 1 of 1
Anatomy of a failure (Z31 coilover adapters)
Recently a customer had an accident that wasn't reported directly, as such these images and discussion are a one sided analysis of what appears to have happened, in an attempt to discern what did or did not fail, since it relates to a product we offer.
So what needs to be made clear as a preword, we were not consulted about the installation, no questions asked, no progress pictures sent, the install was done by the customer alone. The photos of the carnage came by way of third-party. We must assume the customer placed the blame on their poor installation, as they never so much as mentioned it in the off-chance it could help aid product design or be a lesson to creating better instructions.
Now here is the most important of the two photos, it clearly shows the adapter still attached to the coilover bracket, with none of the retaining bolts broken. Also visible is the rollcenter adjuster still attached to the steering knuckle, also apparently undamaged, except the obviously sheared bolts that once held it to the spindle in the second picture.
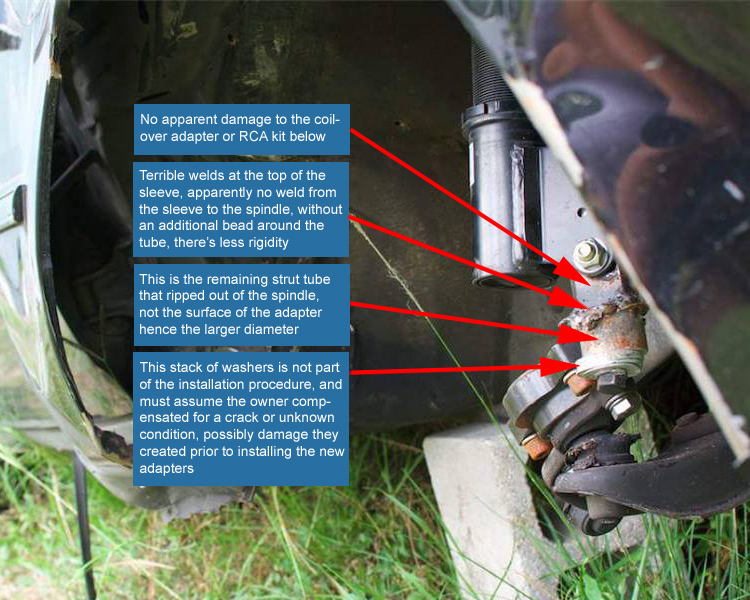
Since we don't know precisely what the car was doing, or what the car did prior to that, we can't know if there was a specific event, or accumulated damage leading up to the disaster. Thus, we have to work backwards.
What we can conclude from above is that the vertical and bending load placed on the adapter and coilover was not the cause of the separation, there is however a lot of oxidation crust on the strut tube surface, and the inner wall of the spindle as seen in the next diagram. That crust suggests the improperly welded tube could have been wiggling inside the cast body of the spindle for some time, and may have destroyed the OEM weld at the very bottom of the tube, which could be seen from underneath.
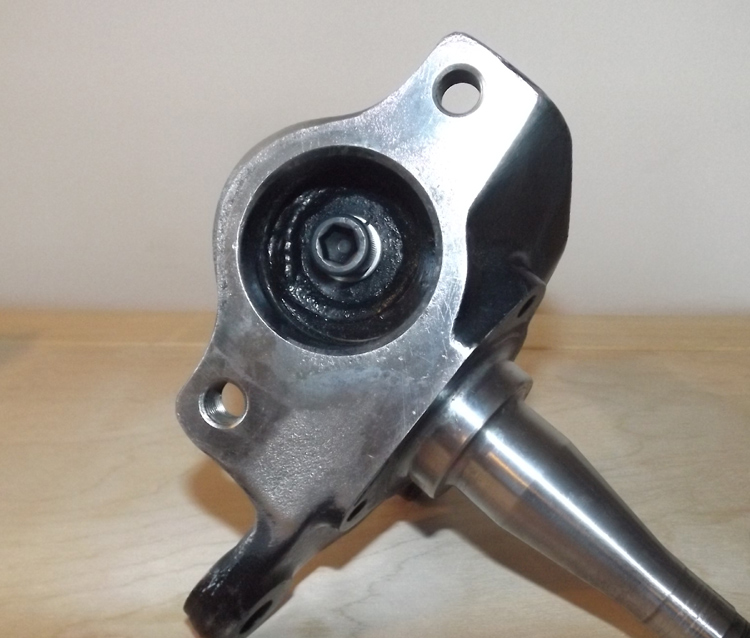
The broken RCA bolts don't specifically indicate anything, as there are several possible reasons for them to shear in this accident alone, and it is even possible they had loosened over time, but were never inspected. If the bolts had loosened, the RCA could have tilted slightly under high load, causing them to snap, which in hard cornering or drifting could detach the spindle from the steering knuckle and RCA, allowing the wheel to jam up against something.
What we know for sure is the bolts can't normally be removed with the steering knuckle still attached, and indeed the heads of those bolts are still present in the above photo, shown with a nice orange coating of rust. It appears the bolt heads haven't dropped form the original position, which indicates there was very likely bending more than tensile force applied to them, forcing some of the threads to press against the RCA in more than one location, holding them in place. This particular RCA kit was the high-grade steel option, and the threads of the bolt likely barely made an impression, but there are no photos of that either.
Now that all suggests the RCA bolts sheared as the result of the wheel remaining attached to the lower control arm, and not attached to the strut, creating the bending moment from below. If the wheel had remained attached to the strut, far less directional load or bending would have been placed on the spindle from above, as the wheel would have been free to move around a lot more. What is more likely is that the failure of the strut tube bottom caused a violent horizontal bending moment by way of rotation, without fully separating initially. In other words everything broke approximately at the same instant.
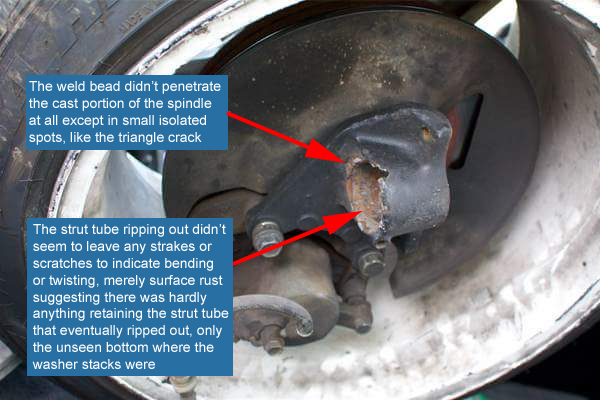
What we can clearly see here is the spindle suffered damage around the top face, where it should have had a proper weld bead with good penetration. The lack of penetration is obvious, but what is not obvious is the intentions of the welder, it isn't clear they were even trying to penetrate.
This may be the hardest part of the installation for a novice, as welding to cast steel requires preheating the areas being welded, if not the entire spindle. Ideally a welder will TIG weld the strut tube to the adapter, ensuring a good bond, creating a watertight seal at the same time, then repeat the procedure between the strut tube and cast spindle body. This creates an excellent buttress against any flex or gaps present between the components.
The only periodic maintenance necessary with this setup is inspecting the numerous bolts holding everything together, especially the bolts around the RCA kit, since they rely entirely on lock washers to stay tightened.
This wasn't a product failure, but a failure of other components caused by poor installation methods, with minor correctable issues compounding over time.
We hope this is illuminating for potential end-users of this kit, and to help separate the fact from fiction.
So what needs to be made clear as a preword, we were not consulted about the installation, no questions asked, no progress pictures sent, the install was done by the customer alone. The photos of the carnage came by way of third-party. We must assume the customer placed the blame on their poor installation, as they never so much as mentioned it in the off-chance it could help aid product design or be a lesson to creating better instructions.
Now here is the most important of the two photos, it clearly shows the adapter still attached to the coilover bracket, with none of the retaining bolts broken. Also visible is the rollcenter adjuster still attached to the steering knuckle, also apparently undamaged, except the obviously sheared bolts that once held it to the spindle in the second picture.
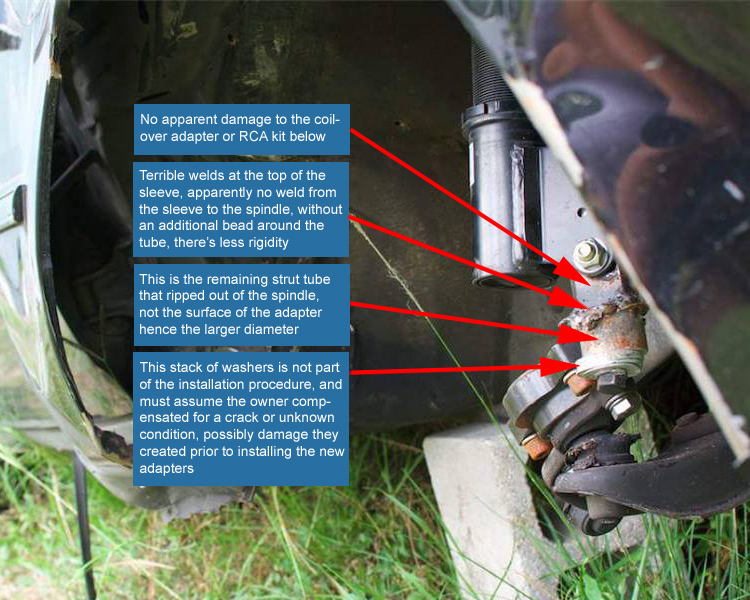
Since we don't know precisely what the car was doing, or what the car did prior to that, we can't know if there was a specific event, or accumulated damage leading up to the disaster. Thus, we have to work backwards.
What we can conclude from above is that the vertical and bending load placed on the adapter and coilover was not the cause of the separation, there is however a lot of oxidation crust on the strut tube surface, and the inner wall of the spindle as seen in the next diagram. That crust suggests the improperly welded tube could have been wiggling inside the cast body of the spindle for some time, and may have destroyed the OEM weld at the very bottom of the tube, which could be seen from underneath.
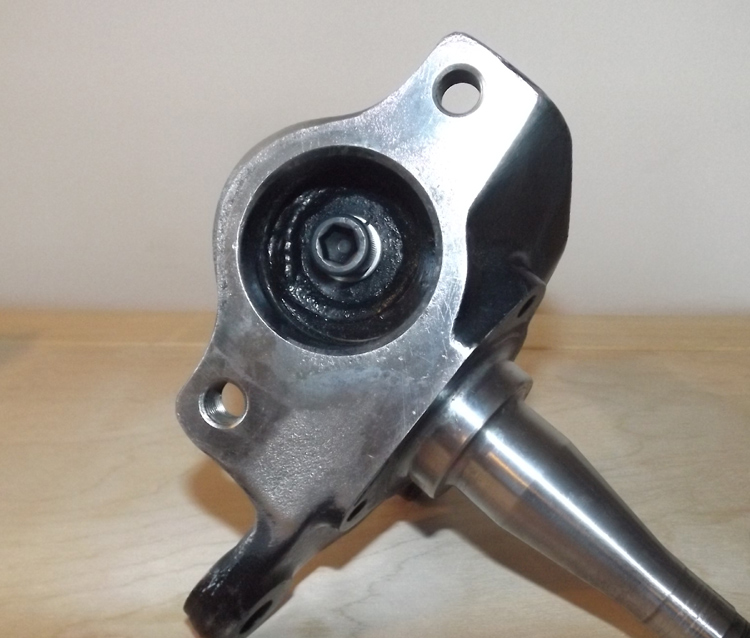
The broken RCA bolts don't specifically indicate anything, as there are several possible reasons for them to shear in this accident alone, and it is even possible they had loosened over time, but were never inspected. If the bolts had loosened, the RCA could have tilted slightly under high load, causing them to snap, which in hard cornering or drifting could detach the spindle from the steering knuckle and RCA, allowing the wheel to jam up against something.
What we know for sure is the bolts can't normally be removed with the steering knuckle still attached, and indeed the heads of those bolts are still present in the above photo, shown with a nice orange coating of rust. It appears the bolt heads haven't dropped form the original position, which indicates there was very likely bending more than tensile force applied to them, forcing some of the threads to press against the RCA in more than one location, holding them in place. This particular RCA kit was the high-grade steel option, and the threads of the bolt likely barely made an impression, but there are no photos of that either.
Now that all suggests the RCA bolts sheared as the result of the wheel remaining attached to the lower control arm, and not attached to the strut, creating the bending moment from below. If the wheel had remained attached to the strut, far less directional load or bending would have been placed on the spindle from above, as the wheel would have been free to move around a lot more. What is more likely is that the failure of the strut tube bottom caused a violent horizontal bending moment by way of rotation, without fully separating initially. In other words everything broke approximately at the same instant.
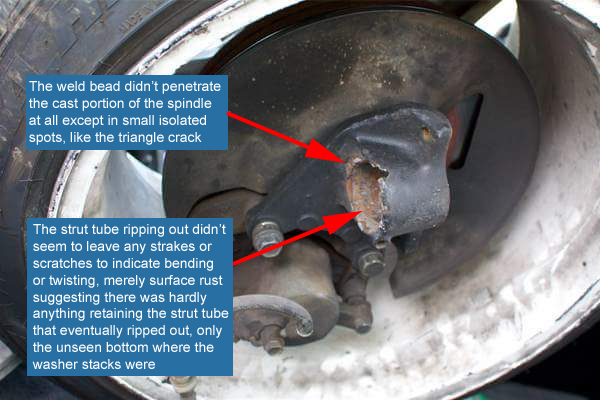
What we can clearly see here is the spindle suffered damage around the top face, where it should have had a proper weld bead with good penetration. The lack of penetration is obvious, but what is not obvious is the intentions of the welder, it isn't clear they were even trying to penetrate.
This may be the hardest part of the installation for a novice, as welding to cast steel requires preheating the areas being welded, if not the entire spindle. Ideally a welder will TIG weld the strut tube to the adapter, ensuring a good bond, creating a watertight seal at the same time, then repeat the procedure between the strut tube and cast spindle body. This creates an excellent buttress against any flex or gaps present between the components.
The only periodic maintenance necessary with this setup is inspecting the numerous bolts holding everything together, especially the bolts around the RCA kit, since they rely entirely on lock washers to stay tightened.
This wasn't a product failure, but a failure of other components caused by poor installation methods, with minor correctable issues compounding over time.
We hope this is illuminating for potential end-users of this kit, and to help separate the fact from fiction.
1 post
• Page 1 of 1
Who is online
Users browsing this forum: No registered users and 0 guests